[ad_1]
Imagine living in a home where the walls are cold to the touch during winter and hot in the summer. The rooms feel drafty, and the energy bills are sky-high. This is a reality for many homeowners, but it doesn’t have to be.
Spray foam insulation can solve these problems, providing a comfortable, energy-efficient living environment. This comprehensive guide will explore spray foam insulation costs, benefits, and long-term savings.
Key Takeaways
- Spray foam insulation costs range from $1,400 to $4,200 on average and are influenced by various factors.
- Professional installation offers efficient completion with specialized equipment and expertise at competitive pricing.
- Spray foam insulation provides up to 50% energy efficiency for long-term savings that can help cover the additional costs.
Exploring the Price Range of Spray Foam Insulation

Homeowners aiming to enhance their home’s comfort and energy efficiency might find it wise to invest in spray foam insulation. The foam insulation cost typically ranges from approximately $1,400 to $4,200, with an average cost of $2,770 USD.
This price range is influenced by various factors, such as:
- The type of insulation
- The material used
- The thickness
- The area of the home to be insulated
A deeper comprehension of the cost spectrum can be achieved by examining the differences between open-cell and closed-cell foam insulation, assessing the impact of thickness, and estimating area coverage.
The Cost Spectrum of Open Cell vs. Closed Cell Foam Insulation
Regarding spray foam insulation, there are two main types to consider: open-cell and closed-cell foam. Open-cell foam insulation is more cost-effective, ranging from $0.50 to $0.75 per board foot, but is less efficient in moisture control. On the other hand, closed-cell foam insulation is denser and provides better insulation but comes at a higher cost, ranging from $1.00 to $2.00 per board foot.
Closed-cell insulation offers advantages over open-cell spray foam insulation, such as being resistant to mold or mildew development, even in high-moisture conditions. Thus, when choosing between the two types, both the cost and the specific requirements of your home should be considered.
Thickness and its Influence on Insulation Cost
The thickness of spray foam insulation is another factor that influences its cost. Thicker insulation offers a higher R-value, which is an indicator of thermal resistance and improved energy efficiency. Closed-cell spray foam insulation has a high R-value. It ranges from 6 to 7 per inch.
The cost of 1-inch open-cell foam typically ranges from $1.00 to $3.00 per square foot, while 3-inch closed-cell foam can cost up to $4.00 per square foot. Selecting the suitable thickness based on your home’s distinct requirements and climate is necessary.
The spray foam insulation cost is calculated per board foot, with prices varying based on type, thickness, and area size. For an area of 100 square feet, the average spray foam insulation cost is between $50 and $75. The cost of painting a home with 3,000 square feet of wall space varies greatly. It could range from $1,320 to $4,500.
It’s important to note that the average cost per board foot for open-cell spray foam insulation typically ranges from $0.50 to $0.75, while closed-cell insulation generally costs $1.00 to $2.00 per board foot. A comprehension of per-board foot pricing aids in making a more accurate estimation of the cost involved in insulating your home with spray foam insulation.
Calculating Your Spray Foam Insulation Investment
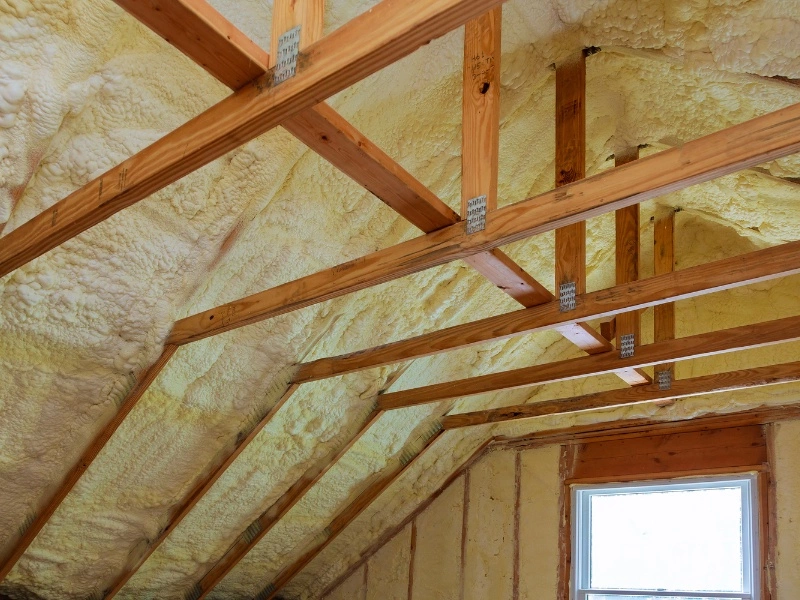
Whether considering a DIY approach or hiring a professional, it’s essential to calculate your spray foam insulation investment accurately. The average costs for DIY spray foam insulation kits are approximately $400 for a 200-square-foot kit and $1000 for a 600-square-foot kit.
On the other hand, the foam insulation cost of professional spray foam insulation can range from $1.55 to $8.00 per square foot. In either case, the total cost will depend on various factors, such as the type of foam, the size of the area to be insulated, the accessibility of the area, the complexity of the project, and the location.
Evaluating each option’s advantages and disadvantages and deciding based on your budget and personal needs is necessary.
DIY Spray Foam Insulation: Costs and Considerations
DIY spray foam insulation kits can be a cost-effective option for homeowners, with prices ranging from $400 to over $1000. However, contemplating the possible risks and challenges related to DIY installation is of utmost importance.
Here are some considerations:
- Improperly installed spray foam insulation can result in water damage from frozen pipes.
- Proper safety measures must be taken, including wearing protective gear and using plastic sheeting to protect surrounding items, which can add an estimated $200 to the overall cost.
- DIY spray foam insulation kits may not be covered by manufacturer warranties.
It is generally recommended to entrust this task to professionals.
Professional Spray Foam Insulation Services
Hiring a professional insulation contractor for spray foam insulation installation offers several advantages, such as:
- Faster and more efficient completion
- Specialized equipment
- Specialized knowledge and expertise
- Warranty
The foam insulation cost of professional installation ranges from $1,400 to $4,200. Labor costs are generally determined based on the project’s scale and the installation’s complexity, with prices ranging from $50 to $100 USD per hour.
Receiving quotes from several contractors assists in price comparison and assures you of a rational estimate for labor costs.
Enhancing Energy Efficiency: The Long-Term Savings of Spray Foam
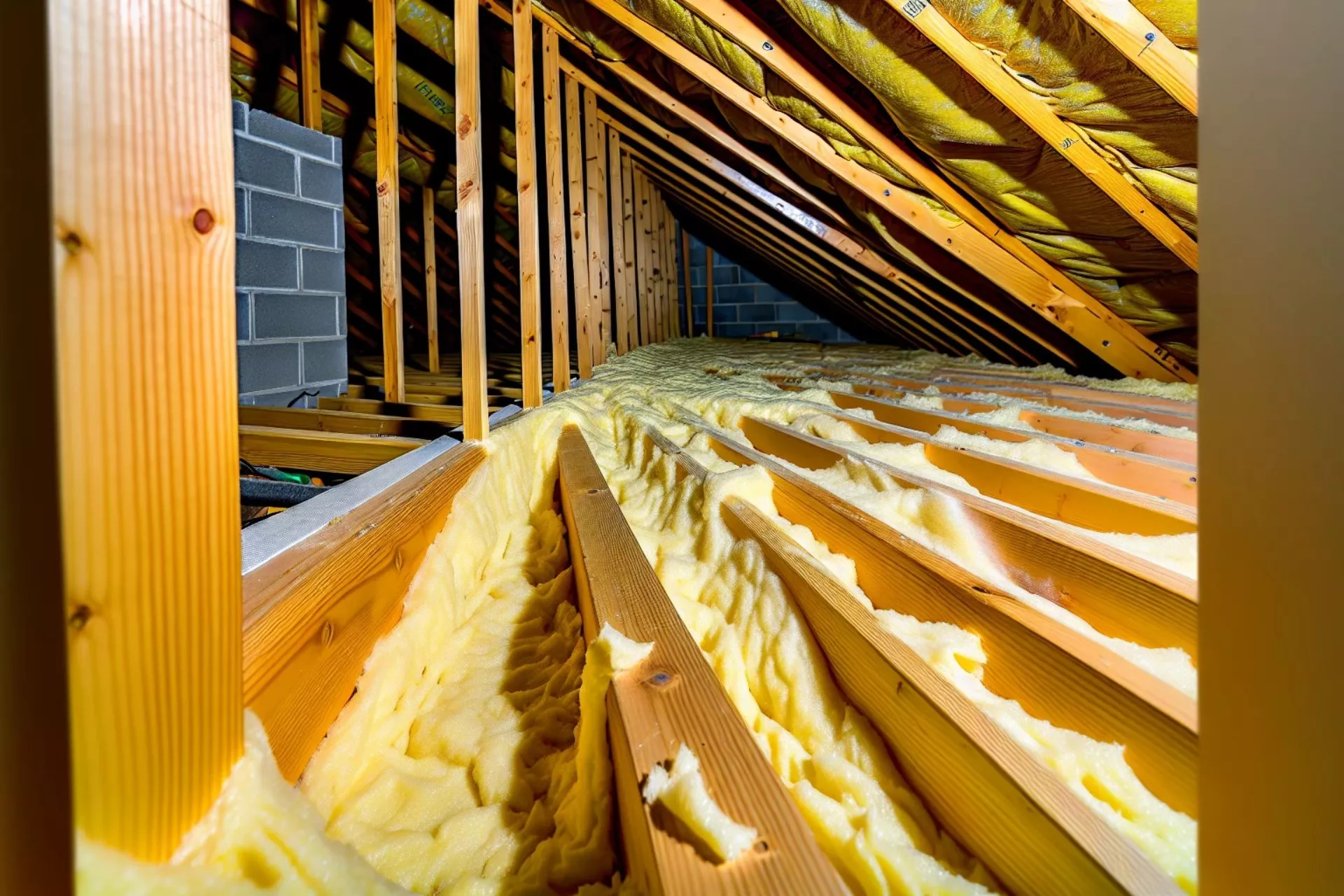
Despite the initial cost of spray foam insulation potentially being higher than conventional insulation options, the long-term energy savings can be substantial. Spray foam insulation offers the following benefits:
- It is up to 50% more efficient than certain other types, such as fiberglass batts or cellulose fibers.
- It has a useful life of up to 80 years, which is up to three times longer than other types.
- By sealing air leaks and providing high R-value insulation, spray foam insulation can lead to long-term energy savings that can help you recover the additional cost within a few years.
Sealing Air Leaks for Lower Energy Bills
Air sealing with spray foam insulation can save up to 40% on energy costs. By creating a tight barrier that prevents the passage of air, spray foam insulation seals gaps and cracks in the exterior air barrier, such as wood sheathing, to eliminate drafts and reduce energy loss in the home.
Prior to air sealing with spray foam insulation, energy consumption patterns may vary depending on the amount of air leakage in the building.
After air sealing, energy consumption patterns are likely to improve significantly. Spray foam creates an airtight seal, blocking any unwanted airflow and reducing heat loss or gain through cracks, gaps, and leaks, resulting in improved energy efficiency and decreased energy bills.
High R-value Insulation for Maximum Thermal Resistance
High R-value insulation, such as closed-cell foam, offers maximum thermal resistance and energy efficiency. The R-value is an indicator of thermal resistance, which is the material’s capacity to impede heat flow. The higher the R-value, the greater the thermal resistance and the better the insulation.
Closed-cell foam insulation achieves maximum thermal resistance through its distinct structure and composition, retaining air within its cells and establishing a barrier that inhibits heat transfer through convection. By using high R-value insulation, you can enhance your home’s energy efficiency and enjoy greater comfort and lower energy bills.
Additional Expenses in the Insulation Process

While budgeting for spray foam insulation, considering the extra expenses that might occur during installation is important. These expenses may include:
- The potential need for old insulation removal
- Vapor barrier installation
- Mold Remediation
- Soundproofing
In the following subsections, we’ll discuss these additional expenses and how they can impact the overall cost of your insulation project.
Mold Remediation Prior to Insulation
If there are indications of mold or if the Environmental Protection Agency suggests it, engaging a professional for mold remediation may be necessary before installing spray foam insulation. Mold remediation involves the removal of mold from a property prior to insulation installation and can cost between $1,500 and $9,000.
Additionally, the cost per square foot for professional mold remediation generally ranges from $15 to $30, depending on the scale and complexity of the mold infestation.
Evaluating the specific situation and consulting specialists to ascertain the necessity for mold remediation before insulation installation is important.
Vapor Barrier Installation and Its Impact on Moisture Control
Vapor barrier installation is essential for moisture control with open-cell foam insulation, as it inhibits moisture from permeating the insulation. The installation of a vapor barrier can have an effect on the overall cost of spray foam insulation, with the cost of installation estimated to be between $0.65 to $2 per square foot.
Considering this extra expense when calculating the overall cost of spray foam insulation is important.
Comparing Spray Foam to Traditional Insulation Options
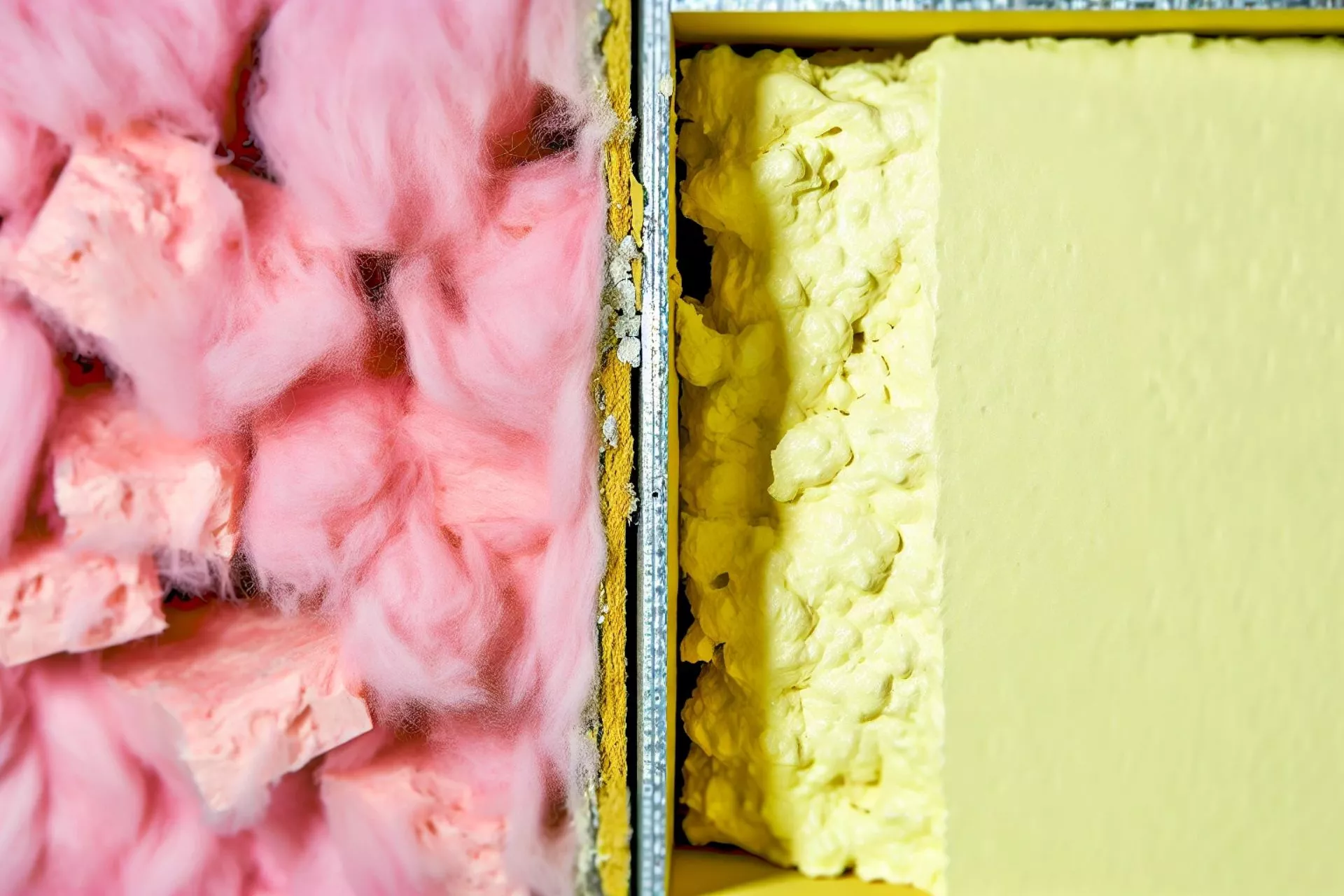
While spray foam insulation holds numerous advantages over traditional insulation options like fiberglass batts or cellulose fibers, considering the variations in cost, R-value, and installation process is vital when making a decision.
In the following subsections, we’ll compare spray foam insulation to traditional insulation options like fiberglass and loose-fill fiberglass, helping you determine the best choice for your home.
Fiberglass Insulation: A Cost-Effective Alternative?
Fiberglass insulation is a popular choice for homeowners on a budget, with an approximate cost of $0.40 to $1.10 per square foot. However, its effectiveness in terms of thermal resistance is generally lower than that of spray foam, with an R-value ranging from 3.1 to 3.4 per inch.
Though fiberglass insulation may be cost-effective in the short term, considering the long-term benefits of spray foam insulation, such as energy savings and enhanced comfort, against the initial cost difference is important.
Loose Fill Fiberglass Insulation: Pros and Cons
Loose-fill fiberglass insulation is another traditional option that can be more eco-friendly than spray foam insulation, as it often contains recycled materials and can be more energy-efficient during production. However, loose-fill fiberglass insulation requires professional installation and may not provide the same air sealing and thermal resistance level as spray foam insulation.
When comparing insulation options, considering both the short-term and long-term benefits and the specific requirements of your home is essential.
Maximizing Home’s Energy Efficiency with Spray Foam
Spray foam insulation can significantly contribute to maximizing your home’s energy efficiency by sealing air leaks, providing high R-value insulation, and diminishing drafts.
In the following subsections, we’ll explore how spray foam insulation can enhance comfort and reduce energy consumption in your home, leading to long-term savings and a more comfortable living environment.
Air Sealing with Spray Foam for Enhanced Comfort
By sealing air leaks and reducing drafts, spray foam insulation can significantly enhance the comfort of your home. Air leaks can be found in various locations, such as:
- the attic
- intersections of materials or components
- floors over crawlspaces
- garages and unconditioned basements
- windows
- doors
- electrical outlets
- plumbing
Using spray foam insulation to seal these leaks, you can create a more comfortable living environment and lower energy bills.
The Role of Spray Foam in Reducing Volatile Organic Compounds
Using low-VOC materials, spray foam insulation can help reduce volatile organic compounds (VOCs) in the home. However, it is essential to note that cutting or trimming the foam during the hardening process may generate dust containing unreacted chemicals, including VOCs.
Proper handling and installation techniques are essential for minimizing potential exposure to VOCs and ensuring a healthier indoor environment.
Navigating the Insulation Installation Process
The insulation installation process can seem overwhelming, particularly for homeowners unfamiliar with the subject. It’s important to:
- Select the right insulation material
- Work with a professional insulation contractor
- Understand the various factors that can affect the cost and effectiveness of the insulation.
In the following subsections, we’ll guide you through the insulation installation process and help you make informed decisions that will result in the best possible outcome for your home.
Selecting the Right Insulation Material for Your Needs
To choose the appropriate insulation material for your needs, consider factors such as:
- Thermal performance
- Moisture resistance
- Fire resistance
- Energy efficiency
- Durability
- Noise reduction
- Environmental impact
- Cost
Climate is another important factor, as temperature and humidity fluctuations can affect the material’s thermal conductivity.
By evaluating these factors, you can select the insulation material that best meets your specific needs and budget.
Working with Insulation Contractors for Optimal Results
Working with insulation contractors can ensure optimal results and adherence to building codes. When selecting an insulation contractor, consider the following factors:
- Licensing and insurance
- Credentials and certifications
- Range of services
- Online reviews and testimonials
- Knowledge and expertise in insulation types
By assessing these factors, you can choose a contractor who will meet your insulation needs effectively.
Furthermore, a professional insulation contractor can ensure compliance with building codes by:
- Having a comprehensive understanding of the codes
- Utilizing materials that meet the requirements
- Employing proper installation methods
- Coordinating with other trades involved in the construction process.
Retrofitting Homes with Spray Foam Insulation
Retrofitting homes with spray foam insulation might be a wise investment, as it can enhance your home’s energy efficiency and comfort. However, the process may involve additional expenses, such as removing old insulation and insulating exterior walls.
In the following subsections, we’ll discuss the process of retrofitting homes with spray foam insulation and the potential costs involved.
Removing Old Insulation: Procedures and Costs
Removing the existing insulation may be necessary prior to installing spray foam insulation. It is important to check this before starting the project. The cost of old insulation removal can vary depending on the type of insulation and the size of the area, with an average cost ranging from $1.00 to $2.00 per square foot.
The removal process involves using a shop vac to vacuum up the insulation, disposing of it in garbage bags, and laying a tarp underneath the bags for convenient cleanup. Proper safety precautions, such as wearing protective clothing, a dust mask or respirator, and using a vacuum with a HEPA filter, should be taken during the removal process.
Retrofitting Exterior Walls with Foam Insulation
Retrofitting exterior walls with foam insulation can improve energy efficiency and comfort in your home. The cost of retrofitting exterior walls with foam insulation is estimated to be between $1.25 and $4.50 per square foot.
The process involves drilling holes into the wall cavity at regular intervals, injecting the foam insulation through the drilled holes, and patching the holes after installation. It is recommended to consult with a professional insulation contractor for a detailed assessment and proper installation.
Insulating Specialized Spaces with Spray Foam
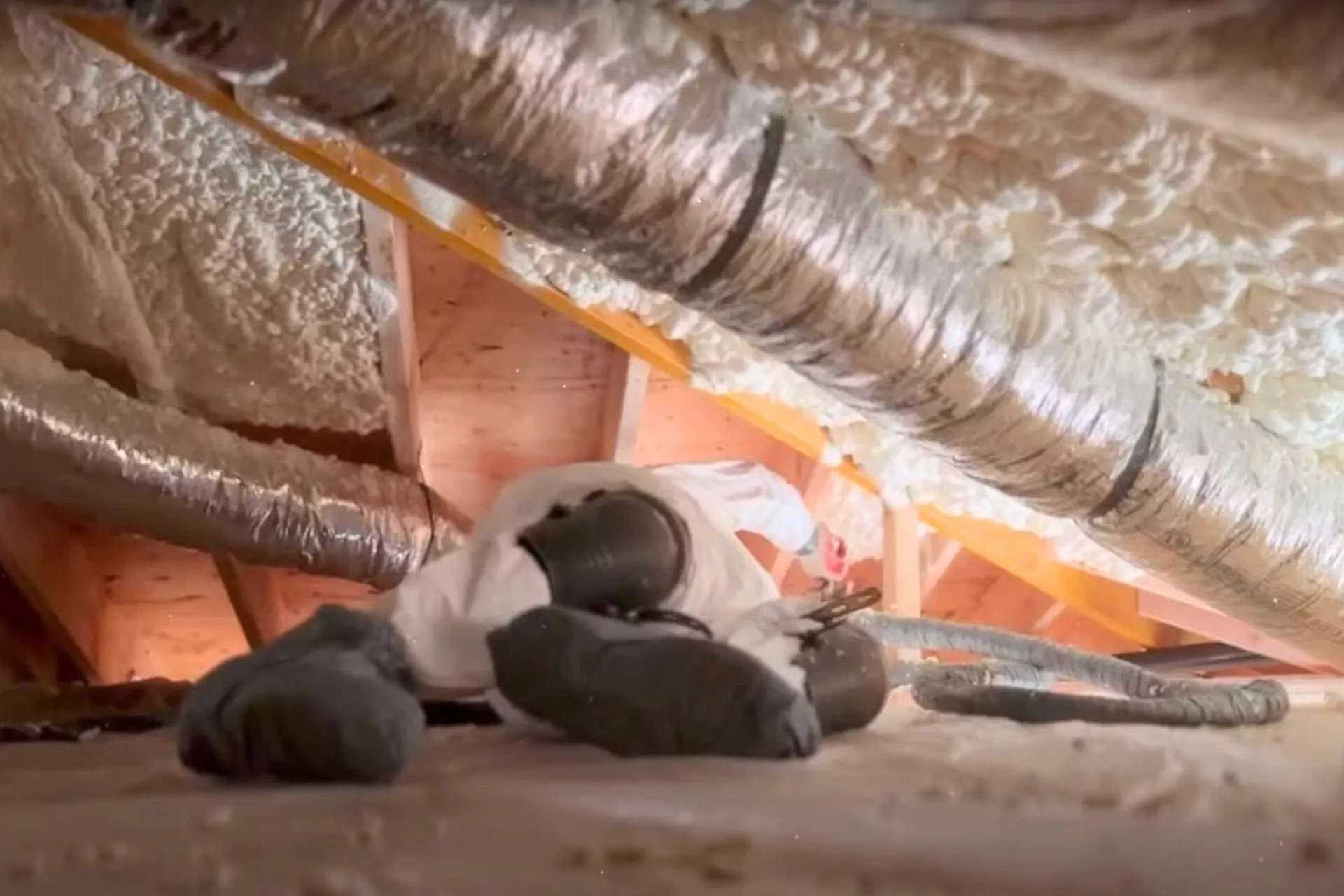
Insulating specialized spaces like crawl spaces and attics with spray foam insulation can be a beneficial investment in improving your home’s energy efficiency and comfort.
The following subsections discuss the challenges and solutions associated with insulating these specialized spaces and the potential costs involved.
Crawl Space Insulation Challenges and Solutions
Crawl space insulation can present challenges like moisture, mold and mildew growth, and air movement. Spray foam insulation can effectively address these challenges by repelling moisture, preventing mold and mildew growth, and creating a tight seal to inhibit air movement.
The estimated cost of adding spray foam insulation to a crawl space ranges from $1,500 to $15,000. By insulating your crawl space with spray foam, you can improve your home’s overall comfort and energy efficiency.
Attic Insulation and Energy Savings
Attic insulation with spray foam can lead to energy savings, with costs ranging from $1,500 to $3,500. By sealing any potential gaps or holes in the roof deck, spray foam insulation can help maintain a comfortable temperature inside the building throughout the year, leading to lower heating and cooling bills, with an average reduction of 40% to 50%.
Installing spray foam insulation in your attic can result in both short-term and long-term benefits, making it a worthwhile investment for homeowners.
Financial Incentives for Installing Spray Foam Insulation
Homeowners enhancing their home’s energy efficiency with spray foam insulation might qualify for financial incentives, including tax credits and rebates. These incentives can help offset the initial cost of spray foam insulation, making it an even more attractive option for homeowners looking to enhance their homes’ comfort and energy efficiency.
It’s important to research available incentives in your area and consult a professional insulation contractor to determine if you qualify for financial assistance.
Summary
In conclusion, spray foam insulation offers numerous benefits, including improved energy efficiency, comfort, and long-term cost savings. By understanding the factors that influence the cost of spray foam insulation, considering DIY vs. professional installation, and exploring financial incentives, homeowners can make informed decisions about the best insulation solution for their needs.
By investing in spray foam insulation, you can enjoy a more comfortable, energy-efficient, and eco-friendly living environment for years to come.
Frequently Asked Questions
How much does it cost to spray foam 200 square feet?
Spray foam insulation for 200 square feet costs approximately $600-$800.
Is spray foam insulation worth the money?
Spray foam insulation is definitely worth the money, as it can save up to 50% on your energy bills with its highly effective heat retention.
Is there a downside to spray foam insulation?
Spray foam insulation can cause roof damage, particularly in areas with cold weather, as it can become susceptible to water vapor damage, which leads to roof rot.
How much does insulating a 24×24 garage with spray foam insulation cost?
On average, it will cost approximately $3600 to $8.650 to insulate a 24×24 garage.
What is the typical cost range for spray foam insulation?
The typical cost range for spray foam insulation is between $1,400 to $4,200.
[ad_2]
Source_link